Hooke’s Law of Elasticity
Hooke’s Law of Elasticity is a fundamental principle in physics and mechanics that describes how a material deforms under the application of force. It states that the strain (deformation) in the material is directly proportional to the applied stress, provided the deformation is elastic and the material’s elastic limit is not exceeded. This law is crucial in fields like mechanical engineering and materials science, where understanding the behavior of materials under load is essential. By integrating principles from the laws of mechanics, Hooke’s Law helps predict how structures will bear weight and respond to various forces. This relationship is typically expressed with the formula F = kx, where 𝐹 is the force applied, 𝑘 is the spring constant, and 𝑥 is the extension or compression of the material.
What is Hooke’s Law of Elasticity?
Hooke’s Law of Elasticity Formula
Here:
- 𝐹 represents the force applied to the material,
- 𝑘 is the spring constant, which quantifies the stiffness of the spring or material,
- 𝑥 is the displacement of the material from its original, undeformed position.
This formula indicates that the force required to deform the material is proportional to the amount of displacement experienced by the material. This relationship holds true as long as the deformation remains within the elastic limit of the material, meaning it will return to its original shape when the force is removed.
Hooke’s Law of Elasticity Example
Stretching a Spring
Scenario: Imagine you have a spring hanging from the ceiling, and you attach a weight to the bottom of the spring. Let’s say the spring has a spring constant (k) of 100 Newtons per meter (N/m), which indicates the stiffness of the spring.
Application of Hooke’s Law: When you hang a weight that exerts a force of 50 Newtons due to gravity, you want to determine how much the spring will stretch.
Using Hooke’s Law Formula: The formula is: 𝐹 = 𝑘𝑥
Where:
- 𝐹 is the force applied by the weight (50 Newtons in this case),
- 𝑘 is the spring constant (100 N/m),
- 𝑥 is the displacement or stretch of the spring we need to find.
Calculating the Displacement: To find 𝑥, rearrange the formula to solve for displacement: 𝑥 = 𝐹𝑘
Plugging in the values: 𝑥 = 50 Newtons/100 N/m=0.5 meters.
Conclusion: This calculation shows that attaching a 50 Newton weight to the spring causes it to stretch by 0.5 meters. This example demonstrates how Hooke’s Law predicts the amount of stretch based on the stiffness of the spring and the force applied. As long as the force does not exceed the elastic limit of the spring, it will return to its original length once the weight is removed. This principle is widely applicable in designing systems that rely on elastic properties, such as vehicle suspensions, mechanical sensors, and various types of spring-loaded devices.
Hooke’s Law of Elasticity Experiment
Conducting an experiment to demonstrate Hooke’s Law of Elasticity is a straightforward way to observe how materials deform elastically under applied forces. Here’s a step-by-step guide to setting up and performing an experiment to explore this law using a spring and various weights:
Materials Needed
- A spring with known spring constant 𝑘k
- A sturdy support (like a retort stand)
- A set of slotted weights
- A meter stick or a ruler for measuring displacement
- A clamp to secure the spring
Setup
- Secure the Spring: Attach the spring to the retort stand using the clamp. Ensure it hangs vertically and freely without any obstructions.
- Initial Measurement: Before adding any weights, measure the natural length of the spring from the point of attachment to its bottom. Record this as the initial length 𝐿0.
Procedure
- Add a Weight: Attach a small weight to the bottom of the spring. Let the spring come to rest so that it stops oscillating.
- Measure Displacement: Measure the new length of the spring 𝐿1 from the point of attachment to the bottom of the weight. Calculate the displacement 𝑥 by subtracting the initial length from the new length: 𝑥 = 𝐿1−𝐿0.
- Record and Repeat: Record the force exerted by the weight (which is equal to the weight’s mass multiplied by the acceleration due to gravity, 𝐹 = 𝑚𝑔) and the corresponding displacement 𝑥. Repeat this step by adding more weights, one at a time, and measure the resulting displacements.
- Maintain Within Elastic Limit: Ensure that the weights do not deform the spring permanently. Stay within the elastic limit to keep the experiment valid under Hooke’s Law.
Data Analysis
- Plot the Data: Create a graph plotting the force 𝐹 on the y-axis and the displacement 𝑥 on the x-axis.
- Linear Relationship: The plot should ideally form a straight line if the spring obeys Hooke’s Law, indicating a linear relationship between force and displacement.
- Determine Spring Constant: The slope of the line on the plot represents the spring constant 𝑘. You can calculate it by the formula 𝑘 = 𝐹/𝑥.
Conclusion
The experiment should demonstrate that the force required to stretch the spring is directly proportional to the distance it stretches, which is the essence of Hooke’s Law. This hands-on activity not only confirms the theoretical aspects of elasticity but also introduces practical considerations like the importance of staying within the elastic limit and understanding material properties.
This experiment is typically performed in educational settings to reinforce concepts in physics and is an excellent demonstration of fundamental mechanical principles.
Hooke’s Law of Elasticity Graph
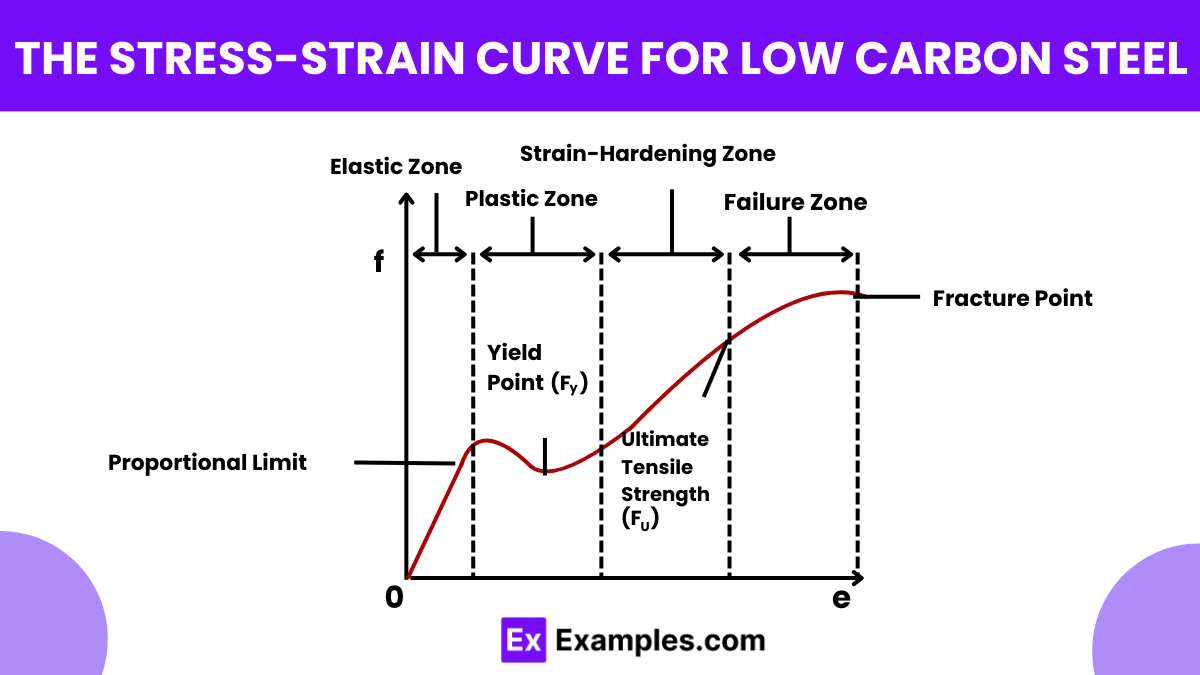
A graph demonstrating Hooke’s Law of Elasticity typically plots force (F) on the vertical axis against displacement (x) on the horizontal axis. For a material obeying Hooke’s Law, the graph is a straight line originating from the origin, indicating a linear relationship between force and displacement. The slope of this line equals the spring constant 𝑘, which represents the stiffness of the spring. The linearity of the graph persists only up to the elastic limit; beyond this point, the material may not return to its original shape, and the graph may deviate from a straight line. This graph is crucial for visually confirming that the force needed to stretch or compress the spring is directly proportional to the extent of its deformation.
Hooke’s Law of Elasticity Extension
In the context of Hooke’s Law, the term “extension” refers to the displacement or deformation experienced by a material (such as a spring) when a force is applied. Hooke’s Law quantitatively describes this extension as directly proportional to the force applied, within the elastic limit of the material.
Formula:
The extension (𝑥) can be calculated using the formula derived from Hooke’s Law: 𝐹 = 𝑘𝑥.
Application:
For instance, if a spring with a spring constant (𝑘) of 200 Newtons per meter (N/m) is subjected to a force of 50 Newtons, the extension (𝑥) can be calculated as follows: 𝑥 = 𝐹/𝑘 = 50 N/200 N/m = 0.25 meters.
Practical Understanding:
This calculation helps in understanding how much a spring will stretch or a material will deform when a certain force is applied. This concept is crucial in designing mechanical systems and structures, ensuring that they can handle the forces they encounter without sustaining permanent deformations.
Hooke’s Law of Elasticity Applications
- Spring Design and Manufacturing: Hooke’s Law is crucial in designing springs used in various mechanical systems like watches, vehicles (suspensions), and electronics (switches). Engineers use this law to determine the specifications of springs, ensuring they perform as expected without exceeding their elastic limits.
- Structural Engineering: In construction, Hooke’s Law helps in determining how building materials will deform under load. This is vital for ensuring the safety and integrity of structures such as bridges, skyscrapers, and beams, which must withstand various forces without permanent deformation.
- Seismology: Seismologists use Hooke’s Law to understand how the Earth’s crust behaves under stress. It helps in modeling the stress and strain relationships in geological formations, which is important for predicting earthquakes and understanding tectonic movements.
- Automotive Industry: The automotive industry applies Hooke’s Law in designing vehicle suspensions that can absorb shocks effectively. By knowing how materials compress and extend under forces, engineers can create systems that improve ride quality and vehicle durability.
- Medical Devices: Hooke’s Law is used in the design of various medical devices, including stents and orthodontic appliances (like braces). These devices must exert precise forces on body parts or tissues to be effective without causing damage or permanent deformation.
- Sports Equipment: The design of sports equipment such as golf clubs, racquets, and even the surfaces of sports courts involve understanding how materials behave elastically. Hooke’s Law helps in optimizing equipment to enhance performance and safety.
- Material Testing: Hooke’s Law is fundamental in material science for conducting tensile and compression tests. It allows researchers to determine the elastic properties of new materials and composites, which is crucial for innovative applications in industries like aerospace, automotive, and electronics.
Hookes Law of Elasticity Advantages and Disadvantages
Advantages
- Predictability: Hooke’s Law provides a simple, linear relationship between force and deformation, which allows for predictable modeling of material behavior under elastic conditions. This predictability is crucial for designing mechanical systems and structures.
- Simplicity: The formula 𝐹 = 𝑘𝑥 is straightforward and easy to apply, making it accessible for engineers and designers without requiring complex calculations.
- Versatility: Despite its simplicity, Hooke’s Law is applicable in a wide range of fields, from structural engineering to medical devices, where understanding elastic behavior is essential.
- Design Optimization: Hooke’s Law helps in optimizing designs to ensure that materials are used efficiently and do not undergo deformations that could lead to failure or inefficiency.
- Material Testing: It provides a basis for material testing, allowing researchers to determine the elastic properties of materials, such as the Young’s modulus, by measuring the stiffness constant 𝑘.
Disadvantages
- Limited to Elastic Range: Hooke’s Law only applies to the elastic region of a material’s stress-strain curve. It does not account for plastic deformations where permanent changes occur in the material structure.
- Non-applicability to Complex Materials: Many modern materials and composites do not exhibit purely elastic behavior and may have non-linear stress-strain relationships, making Hooke’s Law less useful or irrelevant for these materials.
- Inaccuracy in Real-World Conditions: Real-world conditions such as temperature variations, material flaws, and long-term material fatigue can affect the accuracy of Hooke’s Law. It assumes ideal conditions that often do not hold in practical scenarios.
- Oversimplification: While the simplicity of Hooke’s Law is advantageous, it can also be a drawback as it may oversimplify the behaviors of materials under various forces, ignoring factors like shear stress, torsion, and bending.
- Inapplicability to Viscous Materials: Hooke’s Law is not applicable to fluids or any material where viscosity plays a significant role, limiting its use in fluid dynamics or materials science involving viscous substances.
FAQs
Are there any limitations to using Hooke’s Law in complex structures?
Hooke’s Law is fundamentally limited to describing situations where loads and deformations are directly proportional and occur along a single axis. In complex structures subject to multi-axial stresses, more comprehensive models and calculations are needed to accurately predict behavior.
What happens if the applied force exceeds the elastic limit?
If the force applied to a material exceeds its elastic limit, the material will undergo plastic deformation and will not return to its original shape. Hooke’s Law no longer applies once the material is stretched beyond this point.
Is Hooke’s Law applicable to all types of materials?
Hooke’s Law applies primarily to elastic materials that return to their original shape after the force is removed. It does not apply to materials that do not exhibit linear elastic behavior or those that deform plastically (permanent deformation).